Muhammad Rashid Best Project Award
Thanks to the generous endowment given by Dr. Muhammad Rashid and his wife Dr. Fatema Rashid, the Engineering department is able to support and award students for their hard work in their two-semester capstone projects that integrate knowledge acquired throughout their degree.
Spring 2023 First Place #1
Chess Robot (V.I.C.T.O.R)
Team Members
Connor Oldham, John Kreuser, T.J. Miller, Brandon Moberly
Mentor
Dr. Mohamed Khabou
Abstract
V.I.C.T.O.R uses computer vision to map a matrix representation of the board and assigns labels to the pieces detected. The matrix is passed to an internal chess engine, Stockfish 15.1, using FEN string notation to determine a counter move. Once Stockfish determines a move, a string is passed containing information to instruct our mechanical arm to make the desired move.
Spring 2023 Second Place
The Resistor Vending Machine
Team Members
Quin Godwin, Aryn Hightower, Hunter Rose, Kimberly Vissepo
Faculty Mentor
Professor Sam Russel
Abstract
Resistors purchased by the University of West Florida (UWF) arrive on large cardboard spools, requiring instructors and teaching assistants (TAs) to manually count and cut resistors to place in bins and dispense to students. This method is cumbersome, time-consuming, and makes it difficult to track inventory. Students know too well what it is like to set up a lab or project only to find out the resistors selected are incorrect. Resistors are commonly either wrongly placed in labeled bins or misread as the identification strip colors are misinterpreted, like what is thought to be gold is actually brown. The aim of this project is to improve the accuracy and convenience of the disbursement of resistors to students in UWF’s Circuits Lab. The resistor vending machine houses nine identical modules, each with the ability to count, load, cut, and distribute breadboard resistors of various values. Each module holds up to 500 resistors and functions in connection with an LED touch screen to dispense or load the resistor tape. The LED screen displays the number of resistors currently available within the machine and allows the user to choose the amount to be dispensed and cut. The resistor vending machine allows students to save time by dispensing the desired amount of resistors promptly, thus potentially increasing a student's efficiency in coursework and allowing students to study more. The resistor vending machine can increase productivity, save time, improve classroom organization and inventory accuracy, and can be conveniently placed in schools, laboratories, or workshops that use breadboard resistors.
Fall 2022 First Place
Thermostore
Team Members
Bea Almonte, Katie Balent, Nick Newkirk, Eric Woodring
Faculty Mentor
Professor Sam Russel
Abstract
The thermo-store system is a portable refrigeration system designed with medical applications in mind where records are required to verify the in-range temperatures of the products being stored inside. This system regulates temperature down to -1.5 degrees C, and stores recorded temperatures in an SQL database which is accessible remotely. The System provides an audible alarm when the internal temperature is out of range after initially reaching the set temperature. This system is intended to be operated using a 110V AC source but can operate using internal batteries for up to 2 hours during transport/transition periods. Thermo-store also has an internal voltage monitoring system that sounds an audible alarm when the voltage level reaches a prescribed threshold and displays a recharge battery on the screen as well. This system also records the status of the lid to record whether the lid is open or closed. The purpose of this product is to remove the burden of recording temperatures from the user in a medical environment where logging is critical. This product is portable, and it allows transmission of the log as long as the unit is connected to a WiFi source. The primary market of this device would be a hospital operating room environment for when blood that has been typed and screened is checked out for a surgery procedure. In the event that the blood is not used, the device maintains an accurate log so that the blood products may be returned to the blood bank.
Spring 2022 First Place
RoboBoat: An Autonomous Surface Vessel
Team Members
Charles Hostick, Shane Imm, Erik LaBrot, John Osmialowski, Thati Vang, and Aaron Rogers
Faculty Mentor
Dr. Tarek Youssef Elsayed
Abstract
The UWF Marine Robotics Team designed, built, and programmed an autonomous unmanned boat. The robotic boat uses a combination of GPS, LiDAR, IMU, and cameras to detect and navigate its environment. The environmental data is fed into the Robotic Operating System (ROS) where the sensor data is used to determine a navigation solution. A unique feature of this project is the ability to move the boathouse that houses the systems and sensors needed for autonomous operations between a boat and tank platform. This capability allows the team to test both on land and in water. The land testing option will increase the amount of time we can spend testing the vehicle. The team was able to achieve basic autonomous waypoint navigation to include object detection and avoidance.
Spring 2022 Second Place #1
"Forget Me Not" Car Seat Safety Monitor
Team Members
Kyle Stipp, Christian Clark, Jess Keith, Gabriel Roura, Matthew Fulton, Kyle Parker
Faculty Mentor
Dr. Yazan Alqudah
Abstract
There are many child alert systems to choose from currently on the market. Most fall in the spectrum of lackluster reliability all the way to unavoidable annoyance; both result in reduced use and are self-defeating. The system must be reliable and there are times when a child is intentionally left in a car, for example when the parent is filling the vehicle with fuel. This system is designed to have reliable detection of a child, and methods to override the alerts; however, it still monitors for hazardous conditions when overridden. Many children perish or are exposed to heat injury every year and this system aims to prevent them while being affordable, reliable, and user-friendly.
Spring 2022 Second Place #2
Automated Batch Weighing System
Team Members
Carly Ritchie, Hanna Larmore, Cristy Higginbotham, Samara Potter, Bruno Ariza
Faculty Mentor
Dr. Tarek Youssef Elsayed
Abstract
The Auto Batch System is an automated machine that dispenses dry powdered/granular materials such as flour and sugar into a bowl while also weighing said ingredients within 97.5% accuracy. The bowl is first placed on a scale, which will measure the materials dispensed, the scale with the bowl is attached to a conveyor. Once the user types in the amount and the various types of materials needed (i.e. 36 grams of flour) the conveyor will move to the required stations where the materials are dispensed into the bowl. There are three containers in the system so each recipe can have a variation of three different materials. Using the screwable cap on the top of the container a user can easily refill or change the material to what they want; while also needing to update the app to account for the change. This system is designed for a home setting but is scalable for an industrial setting as well. The Auto Batch System's purpose is to reduce worker shortages and limit contact with potentially hazardous materials.
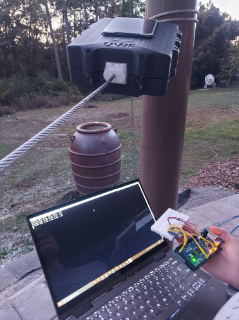
Fall 2021 First Place
Power Line Data Acquisition System
NO VIDEO
Team Members
Jodie Welch, Chance Bellflower, Sam Brown
Faculty Mentor
Dr. Bhuvana Ramachandran
Abstract
Dynamic line rating gives power system operators and utilities the ability to expand the capacity of the existing grid. We designed a two-module system that will give power system operators the ability to track conductor sag and weather conditions in real-time, allowing the implementation of dynamic line rating based on collected data. A line-mounted divide makes use of an inertial measurement unit (IMU), an infrared temperature sensor, and a light-detecting and ranging sensor (LiDAR) to collect data. This data is then reported via radio transceiver to the grand module. Software systems were programmed using MATLAB that takes the angle recorded by the IMU and plots the catenary curve of the conductor, as well as the maximum allowed curve based on NESC clearance requirements and the maximum operating temperature allowed for the type of conductor. This program can also provide graphs of conductor temperature and ambient temperature over time. Lastly, based on the data collected, an adjusted allowable load will be provided. This will allow system operators the ability to increase the capacity of lines and thus reduce transmission system overloading.
Fall 2021 Second Place
Automatic Aluminum Foil Dispenser
Team Members
Grant Ghesquiere, Keith Dang, Braxton Mullarkey, Christian Page, Nathan Simon
Faculty Mentor
Dr. Mohammed Khabou
Abstract
A need was identified for a machine to automatically cut and dispense aluminum foil sheets for use in hair salons to expedite hair dye and highlight services. The device accepts a standard-size roll of aluminum foil and automatically cuts and dispenses aluminum pieces in the amounts and sizes specified by the user. An Arduino microcontroller was selected to control a series of stepper motors that operate rollers and a cutting mechanism and produce foil sheets based on the user input from an LCD display screen. The Arduino was coded to display a user interface on the LCD screen and allows the user to select from several preset lengths of foil and the desired number of sheets to be produced. This basic design, as produced, has the potential for expansion into other trades, including the food service industry.
Spring 2019 First Place
2019 IEEE SoutheastCon Hardware Competition
Team Members
Andrew Petrovsky, Michael Wagner, Dustin Williams
Faculty Mentor
Dr. Andreas Fuchs
Abstract
Space debris, and the threat it poses to current and future exploration is the theme for the IEEE SoutheastCon 2019 Hardware Competition. The goal of this project is to design and build an autonomous robot that will traverse an orbital field and remove debris from the orbital path while avoiding specific obstacles. The robot is divided into three subsystems: locomotion, navigation, and debris capture. The locomotion subsystem employs motors with encoders controlled via a microcontroller to perform precise movements. Navigation is based around a scanning LiDAR sensor coupled with Simultaneous Localization and Mapping (SLAM) algorithms which enable the robot to map its environment and orient itself in real time. Debris capture is accomplished mostly through behavior, with a recessed skid plate that can accumulate objects as exhaustive searches of the field are made.
Fall 2018 First Place
Machine Head Functionality Testing Station
Team Members
Kelly Flack and Conner McCreless
Faculty Advisor
Dr. Bhuvana Ramachandran
Abstract
The project involves the design of a testing station to be incorporated into the production line of the GE 2.X Machine Head. The testing station is capable of delivering power to the Machine Head without many intermittent steps and allows the testers on the production line to be closer to the unit for faster routing of connections and quick emergency stop if a problem arises. The project was a collaboration with GE Renewable Energy in Pensacola.
Second Place
IHMC Underwater Data Collection
Team Members
Andre Serafim, Murilo Basso, Harrison Payne, and Joseph Timbang
Faculty Advisor
Dr. Yazan Alqudah
Abstract
The project is an underwater data collection device overseen by IHMC. The purpose of the device is to use a blue laser as a medium for data transfer such that temperature, imaging, current, and so on. The data can potentially be received from artificial reefs and recorded without any manual effort. Such a device has only been somewhat completed (in the sense that the project had a different goal, but similar application) once at MIT under an essentially limitless budget. One of the goals for this device was to recreate MIT’s success on a significantly scaled budget. As such, research was made into methodology on how to model such a system.
Spring 2018 First Place
Design of a Fully-Autonomous Robot Platform
Team Members
Asma Al-Selwadi, Steven Lewis, Oanh Nguyen
Faculty Advisor
Dr. Mohamed Khabou
Abstract
The IEEE Southeastcon Hardware Competition dictates that a fully-autonomous robot platform will be simulating the role of a pirate with the purpose of reading a treasure map and successfully completing its journey to retrieve the treasure chest. The robot will initially be placed onto its “pirate ship” where it will receive an IR signal that determines the path that the robot must follow. At various points of the path, the robot will have mechanical tasks, such as pushing a button, applying pressure to a pad, raising a flag, and finally lifting and storing the “treasure chest” and bringing it back to the ship.
Second Place
Design of a Wall Painting Robot
Team Members
Christopher DeLauder, Andrew Jones, Stephen Proud, Sam Cobb, Jacob Rea, Kayla Riley
Faculty Advisor
Mr. Richard Landry
Abstract
The capstone team designed an interior wall painting robot. The robot was built to a ½ scale and was able to paint a ½ scale mock-up room with walls 4 feet in height and 8 feet in width. The wall painting robot consists of a mobile robot base equipped with a painting mechanism and paint sprayer. The project assumes basic preparations will be completed beforehand, such as the moving of furniture to the center of the room, the masking of trim and the laying down of appropriate drop cloths.
Fall 2017 First Place
Design of a Fully Autonomous System with a
User-interface Web Platform
Team Members
Everette Petsinger, Taylor Whalen, Kathryn Torre, Winston Riley, Adam Mooers
Faculty Advisor
Dr. Mohamed Khabou
Abstract
The intended goal of this project is to design, build, and test a fully autonomous system with a user-interface web platform. The automated system incorporates all systems required for self-driving including braking, steering, and acceleration. Braking and steering are electromechanically controlled with actuators connected to a real-time management system. There is a GPS system for navigation along a pre-planned route. C.A.R.T., short for Computerized Autonomous Robotic Transportation, aims to provide a more convenient transportation option for urban commuters. Commuters can request and manage rides through a complimentary mobile web app. This project is intended to prevent DUI’s, allow safe travel for handicapped users, and provide personalized transportation routes for busy city travel.
2nd Place
Design of an Autonomous Lawn Mower
Team Members
Kyle Chisum, Evan DeBusk, Corey Stinar, Devin Wisdom
Faculty Advisor
Dr. A. Fuchs
Abstract
The goal of this project is to reduce the annual number of mower blade injuries while minimizing the physical stress required to mow a lawn for at-risk health populations. Along with safety, we believe that there is room for improvement in both quality and price based on comparable autonomous lawn mowers on the market today. To accomplish this goal, a fully autonomous lawn mower capable of navigating a lawn purely with GPS coordinates, derived from an RTK unit, which can maintain safety through multiple sensors was produced.
Spring 2017 First Place
Design of a Remotely Operated Power Line Inspection Tool
Team Members
Bryce Hagar, Wydrick Hill, Sean Miller, Ruben Ramirez, and John Wimberly
Faculty Advisor
Dr. Mohamed Khabou
Abstract
Inspecting power lines for quality and remaining lifespan is time-consuming and costly for power companies worldwide, but this action is imperative for safety and preventing outages. The design of a robot to traverse distribution lines allows a remote operator to conduct a detailed inspection on miles of lines – all from a secure location. With the ability to easily mount this robot and record video from both sides of the line, power companies will be able to provide their lineman a safer working environment and their customers a greater power reliability and reduced costs.
Second Place
Design of a Smart HVAC Control System
Team Members
David Shearlock and Jonathan Nix
Faculty Advisor
Dr. Bhuvana Ramachandran
Abstract
The modern heating ventilation and air conditioning (HVAC ) systems usually rely on a temperature measurement from a single location to control an entire building, or at least a large portion or zone of the building. More precise control of the system is required to improve user comfort and potentially reduce the power demands of HVAC systems. By designing a smarter control unit capable of utilizing an array of temperature and humidity sensors, the control unit directs valves to regulate air flow into or away from a zone thereby increasing personal comfort and reducing unneeded air conditioning to areas where the desired conditions have already been met. This project utilizes a Raspberry Pi microcontroller to receive data from the temperature sensors and relay commands to servo-controlled in-duct dampers, as well as stepper motor controller vent registers. The system was tested inside a multi-room demo home and was shown to provide an evener temperature distribution compared to the traditional single sensor/control system.